What's A Recessed Plate Filter Press?


본문
Recessed plate filter press: suitable for processing concentrated suspension, the cake may be discharged continuously throughout the process, which improves manufacturing effectivity. In brief, the necessities for stable-liquid separation in industrial production might be met using recessed plate filter presses, which rapidly and efficiently separate strong particles from liquids in suspension to acquire a dry cake and a transparent filtrate. KUOSI affords a wide range of filter presses, as well as sludge dryers, dosing programs, blowers, disinfection methods, and wastewater screens. If in doubt, come and seek the advice of us. Filling: The slurry or suspension is pumped into the filter press by means of the feed inlet. The filter press is initially open, allowing the slurry to move into the house between the filter plates. Filtration: As soon as the filter press is filled, it's closed by making use of hydraulic filter press manufacturers strain. This stress pushes the filter plates and frames together, compressing the slurry and forcing the liquid component to move by the filter cloth while retaining the strong particles as a cake. Dewatering: As the filtrate passes by the filter cloth, the solid particles accumulate on the floor, forming a cake. Key gear and programs, such as course of tanks, process piping methods, and process structural help methods, must be sufficient for the general system design life. Process gear elements, equivalent to sensors (e.g., pH, degree, conductivity, etc.), will sometimes have shorter equipment-specific design life with deliberate replacement intervals within the general course of line/system design life.
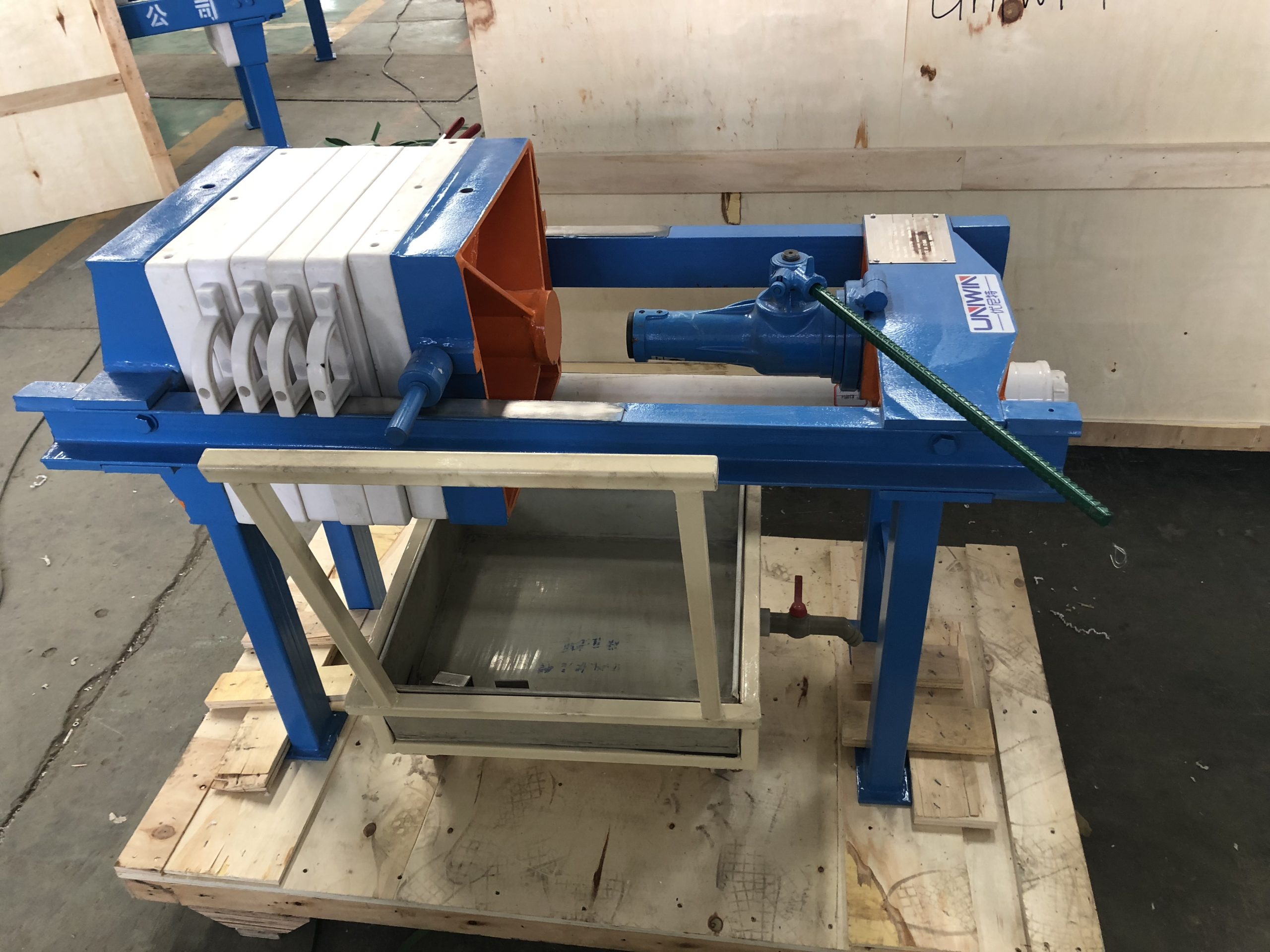
High filter press efficiency: By increasing the area of the filter cloth and reducing the depth of the filter press chamber, the filter press efficiency is increased and strong-liquid separation is realized. Wide range of utility: The recessed chamber filter press is appropriate for treating all kinds of suspended solids with excessive focus, such as sludge, mud, chemicals, minerals, foodstuffs and so on. Impellers are the main stirring units in mechanical mixing tanks. The choice of impeller depends on the vessel form and measurement, the mixture’s viscosity, and the specified rotational speed. Baffles are flat, vertical strips positioned along or close to the vessel walls to forestall vortexing and unbalanced fluid forces on the rotating shaft. The standard is to have 4 equally spaced baffles in a tank if they are wanted (baffles are usually not needed for viscous mixtures). The pictures under are examples of mechanical mixers in use. The pictures to the left show impellers being utilized in wastewater remedy plants. Mixers are utilized in de-nitrification and disinfection processes.
As soon as the test is completed the press is opened, the filter cake is removed, and cake samples are taken. Through the cake release it is important to notice how the cake launched and the overall floor condition of the filter cloth. Cake launch is often somewhat better on a bigger press but when there's poor release on the take a look at unit the release on the bigger unit can be poor. The two criteria for deciding on a cloth are the preliminary high quality of the filtrate and cake release. The hydraulic ram (D) moves the follower (E) in opposition to the stack of filter plates (F) closing the press. The ram continues to apply strain of sufficient force to counteract the high inner compaction pressures. The top stock (G) and tail stock (H) are held in place by specially engineered aspect rail helps bars (I). The filtrate passes through the filter cloth and is directed by channels in the plates and drain ports (J) to the pinnacle inventory for discharge.
댓글목록0